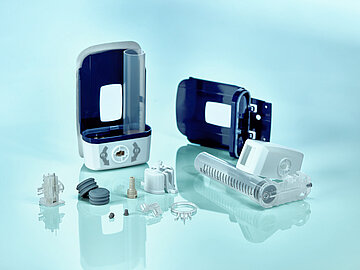
- Arzneimittelabgabe
- Artikel
- Lesezeit: 5 min
Herausforderungen in der Entwicklung von tragbaren Geräten zur Medikamentenverabreichung
Tragbare Geräte zur Verabreichung von Medikamenten können die Lebensqualität von Patienten erheblich verbessern. Sie basieren auf langlebigen Plattformlösungen und erfordern hochmoderne Einwegkomponenten, um sicherzustellen, dass die Patienten genau die erforderliche Dosis des formulierten Medikaments erhalten.
Eine weit verbreitete Form von tragbaren Geräten zu Medikamentenverabreichung sind Insulinpumpen, die Diabetikern eine komfortablere Art der Injektion ermöglichen. Für Medtech-Hersteller ist es entscheidend, bereits in einem frühen Stadium an Entwicklungsprojekten für solche Geräte beteiligt zu sein, um die Designanforderungen und die notwendigen Herstellungsprozesse aufeinander abzustimmen. Das sind die Herausforderungen bei der Entwicklung von tragbaren Geräten zu Medikamentenverabreichung, bei deren Bewältigung ein erfahrener Medizintechnikhersteller Ihnen helfen kann.
Medizinische Wearables: Was sind tragbare Geräte zur Medikamentenverabreichung?
Unauffällig am Körper getragen, vereinfachen sogenannte medizinische Wearables das Leben vieler Menschen. Fitness- und Wellness-Tracker, die am Handgelenk oder als Brustgurt getragen werden, um die Vitaldaten des Körpers aufzuzeichnen und auszuwerten, sind zum Beispiel sehr weit verbreitet.
Eine weitere Form medizinischer Wearables, die immer gefragter werden, sind tragbare Geräte zur Verabreichung von Medikamenten, wie z. B. Insulinpumpen für Diabetiker. Diese medizinischen Geräte werden entweder an einem Gürtel befestigt oder mit Hilfe eines Pflasters direkt am Körper getragen (On-Body-Geräte). Sie verfügen über ein verbautes Infusionssystem und sind für Therapien vorgesehen, die eine regelmäßige subkutane Verabreichung eines formulierten Medikaments erfordern. Die Medikamente können dadurch zeit- und ortsunabhängig verabreicht werden. Moderne Geräte verfügen über intelligente Verbindungen zu digitalen Messgeräten oder Smartphones. Sie bieten den Patienten mehr Sicherheit, Flexibilität und Komfort, was sich positiv auf ihre allgemeine Lebensqualität auswirkt.
Bestandteile von tragbaren Geräten zur Medikamentenverabreichung
Tragbare Geräte zur Verabreichung von Medikamenten bestehen häufig aus zwei Komponenten: Einem wiederverwendbaren elektronischen Aktivator als Gerätebasis, der über längere Zeiträume genutzt werden kann, und ein Einwegmodul oder eine Einwegeinheit, die in kürzeren Abständen ausgetauscht werden kann.
Kernelemente der maßgeschneiderten Einwegmodule sind:
- Der Medikamentenkanal – Die Verbindung aus Infusionsset, Kanüle, Mikroschlauch und Schlauchverbinder
- Die Pumpeneinheit
- Das Reservoir
- Das Nadeleinführsystem
Der Medikamentenkanal in tragbaren Geräten zur Medikamentenverabreichung
Für die Entwicklung und Produktion von kundenspezifischen Einwegeinheiten in tragbaren medizinischen Geräten wird umfassendes Know-how in verschiedenen Herstellprozessen benötigt. So können die notwendigen Prozesse in Einklang gebracht werden und ein passgenaues und gebrauchsfertiges Produkt für die individuelle Geräte-Plattform entwickelt werden.
Der Medikamentenkanal ist ein entscheidendes Element innerhalb des gesamten tragbaren Geräts zur Medikamentenverabreichung. Für die Entwicklung und präzise Herstellung dieses maßgeschneiderten Fluidpfads, der das Medikament durch die tragbaren Geräte leitet, ist ein umfassendes Know-how in verschiedenen Herstellungsprozessen erforderlich. Der Hersteller dieser medizinischen Polymereinheiten muss alle notwendigen Produktionsprozesse genau aufeinander abstimmen und dafür sorgen, dass passgenaue und gebrauchsfertige Produkte für die jeweilige Geräteplattform entwickelt werden.
Das Medikamentenkanalsystem, der so genannte Fluidpfad, vereint eine Gruppe von Einwegkomponenten zum Transport des Medikaments in medizinischen Wearables zur Medikamentenverabreichung.
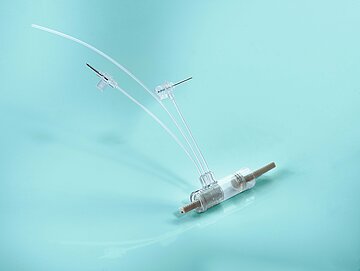
Allein die Herstellung des Medikamentenkanals, der das komplette Infusionssystem des Medizinprodukts darstellt, erfordert umfangreiches und vielschichtiges Produktionswissen. Viele der Einzelkomponenten werden im Spritzgussverfahren hergestellt, während die flexiblen Schläuche im Coextrusionsverfahren produziert werden, um eine bestmögliche Biokompatibilität zu gewährleisten.
Medizinische Wearables: Warum Sie co-extrudierte Schläuche verwenden sollten
Durch den Einsatz der Coextrusions-Technologie für die Produktion der flexiblen Schläuche können Wechselwirkungen zwischen dem Medikament und dem Material ausgeschlossen werden. Die äußere Schlauchschicht aus Polyurethan (PUR) sorgt dafür, dass die Schläuche in den Geräten optimal verklebt und sterilisiert werden können. Die innere Schicht besteht aus Polyethylen (PE), einem inerten Material mit sehr guter Medikamentenverträglichkeit. Bei pharmazeutischen Anwendungen, die in direkten Kontakt mit Arzneimitteln kommen, ist eine sehr sorgfältige Auswahl der verwendeten Materialien unerlässlich.
Das Medikamentenreservoir mit Kolbenstopfen - Für hochpräzise Dosierung in tragbaren Medikamentenverabreichungsgeräten
Bei der Selbstmedikation durch medizinische Geräte erwartet der Patient, dass das Medikament in der exakt benötigten Dosierung abgegeben wird. Deshalb benötigt das Reservoir im tragbaren Medizinprodukt einen Kolbenstopfen mit hervorragenden Gleiteigenschaften. Um perfekte Gleiteigenschaften zu gewährleisten, wird medizinischer Gummi, TPE oder Silikon im Spritzgussverfahren in die gewünschte Form gebracht. Der Kolben wird, wie alle anderen benötigten Polymerelemente, unter Reinraumbedingungen nach ISO-Klasse 7 hergestellt.
Tragbaren medizinischen Geräte: Die Weiterverarbeitung und Montage von Anfang an im Blick
Die Sekundärproduktion spielt auch im Bereich von tragbaren Geräten zur Medikamentenverabreichung eine wichtige Rolle. Im Medikamentenkanal wird der Mikroschlauch mit Hilfe von UV-Verklebung mit den Anschluss-Komponenten verklebt. Für die subkutanen Injektion wird die Injektionsnadel silikonisiert. Einem ähnlichen Vorgang kann auch das Medikamentenreservoir unterzogen werden, um optimale Gleiteigenschaften zu garantieren. Grundsätzlich gilt: Es soll nur so viel Silikonöl verwendet werden, wie für eine gleichmäßige Applikation notwendig ist.
Zusätzlich wird auf das Reservoir aus Polypropylen (PP) im Tampondruck-Verfahren die gewünschte Mengen-Skala aufgedruckt. Die Seriennummer und die Hinweise zur korrekten Platzierung des Kartuschen-Adapters auf dem Pumpengehäuse müssen abriebfest sein, daher werden diese Beschriftungen per Lasermarkierungsverfahren aufgebracht.
Fazit
Frühzeitige Zusammenarbeit bietet Prozesssicherheit bei der Entwicklung und Produktion von tragbaren medizinischen Geräten
Wenn alle wesentlichen Produktions- und Montageschritte unter einem Dach stattfinden, haben Medizingerätehersteller weniger externe Berührungspunkte und dadurch mehr Prozesssicherheit. Durch einen einzigen Ansprechpartner für alle notwendigen Produktionsschritte können Projekte wesentlich an Effektivität gewinnen. Bewährtes Know-how in einer Reihe von Fertigungstechnologien sorgt dafür, dass bereits in der frühen Design- und Entwurfsphase auf die Machbarkeit der Prozesse geachtet wird. Besonders Hersteller aus der pharmazeutischen Industrie haben besondere Anforderungen an das Projektmanagement in der Zusammenarbeit, die Zertifizierung der Produktionsstätten und Erfahrung in der Validierung.