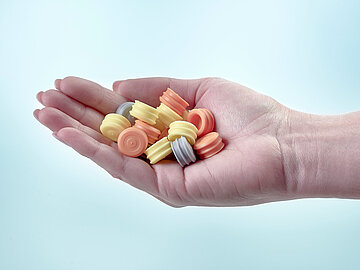
- Development
- Article
- Reading time: 5 min
Pure Silicone Solutions for Next-Gen Drug Delivery
The drug delivery market includes a wide range of products and solutions for administering medications—from simple ampoules and standard syringes to sprays, inhalers, and complex multi-chamber systems for advanced active ingredients. Most of these products have traditionally relied on seals and stoppers made of rubber. This material has proven itself over time and remains an integral part of modern medicine. However, with the growing use of biopharmaceuticals, the demands on drug delivery have increased significantly. Conventional systems using rubber seals or stoppers are increasingly reaching their limits—particularly when it comes to storing sensitive active ingredients.
Reliable Storage – Even at Ultra-Low Temperatures
Take a typical example: ultra-low temperature (ULT) storage at -70 to -80 °C. This method is widely used for biopharmaceuticals—especially for many mRNA vaccines that have been deployed globally since the COVID-19 pandemic. These and other biological molecules, such as biotechnologically produced enzymes and proteins, must be stored at very low temperatures to maintain their activity over time.
Drug delivery solutions for temperature-sensitive biopharmaceuticals must therefore be designed for ULT storage—without compromise. Otherwise, the use of mRNA vaccines and many other modern biopharmaceutical applications would be virtually impossible. This has direct implications for system developers, who must avoid using traditional rubber seals and stoppers. The reason: rubber becomes brittle at low temperatures, develops cracks, and loses its shape. Drug delivery systems for ULT applications must therefore be made from materials that meet storage requirements even at -80 °C—such as silicone.
In response, RAUMEDIC AG has developed a microbiologically pure silicone that meets the high demands of modern biopharmaceuticals. This special material is increasingly being used in prefilled drug delivery systems. Syringe stoppers for administering highly potent medications are already made from RAUMEDIC silicone. This material, which is even listed as a master file with the FDA, offers numerous advantages—not only in terms of thermal tolerance but also chemical properties, product-specific geometries, and more.
Perfect Handling Without Compromise
A closer look at RAUMEDIC silicone reveals that it features very low breakaway forces and low sliding friction. This is particularly important for syringes, where medical professionals have long struggled with the so-called stick-slip effect.
The stick-slip effect, caused by the material-specific friction resistance of the stopper, can cause the syringe plunger to jerk or slip uncontrollably during injection. In extreme cases, accurate dosing becomes a gamble. By fundamentally reducing the stick-slip effect, everyday processes in hospitals and clinics can become significantly more efficient and reliable. Expensive and highly effective medications like biopharmaceuticals can also be dosed more precisely.
Avoiding Contamination
To reduce the stick-slip effect and lower glide forces, most manufacturers add special lubricants such as silicone oil or other substances. While this makes the stopper slide more smoothly, it also introduces the risk of the lubricant mixing with the medication and altering its effect. In extreme cases, this can have serious consequences—especially for biopharmaceuticals.
RAUMEDIC silicone has a clear advantage here as well: thanks to its excellent glide and breakaway properties, users can often completely avoid lubricants or use only minimal amounts to ensure reliable handling.
Another issue is extractables—substances that rubber naturally releases under certain conditions. If these substances leach into the medication, contamination is inevitable. Pure silicone, on the other hand, releases significantly fewer extractables.
Given these factors, silicone stoppers and seals are ideal for administering biopharmaceuticals. These active ingredients are derived from living organisms and are typically very sensitive. Most biopharmaceuticals consist of complex molecules and can be damaged by simple physical or chemical influences, high temperatures, or even light. Drug delivery devices must be designed from the outset to meet these special requirements—including the use of materials that minimize the risk of contamination from extractables, lubricants, or other substances.
Precise and Clean: Custom Solutions via Silicone Injection Molding
In addition to the material properties mentioned, silicone seals and stoppers offer another major benefit: the ability to create more complex geometries. These can be manufactured with high precision using silicone injection molding. RAUMEDIC relies on product-specific designs rather than standard solutions. This strategy enables the production of components for modern drug delivery systems that eliminate the risk of leakage from the outset. As a result, expensive and highly effective medications—including many biopharmaceuticals—can be dosed with minimal dead volume, even in prefilled systems stored for extended periods.
Modern silicone injection molding is ideally suited for producing sophisticated components for advanced drug delivery systems. In contrast, rubber stoppers are still often punched from simple compression-molded sheets, which limits design flexibility and increases particle contamination.
Ready for the Future: A Clear Case for RAUMEDIC
RAUMEDIC impresses not only with its biocompatible, hypoallergenic, temperature-resistant, shape-retaining, and highly durable silicone but also with its customized solutions. The Bavarian company follows a “freedom of design” principle, developing its silicone stoppers and seals according to individual requirements—with highly precise and, if needed, complex geometries. Fully automated injection molding takes place in ISO Class 7 cleanrooms—with optional 100% quality control and fully automated packaging. This minimizes human contact with the product.
There is no doubt: RAUMEDIC’s seals and stoppers are perfectly suited for pharmaceutical and medical technology applications. In many cases, they outperform comparable rubber-based solutions. In fact, RAUMEDIC is setting new standards in drug delivery with consistently high quality, a clear focus on patient safety, and efficient medical processes.
With the growing use of biopharmaceuticals and the rapid expansion of prefilled systems, pure silicone syringe stoppers are becoming increasingly important. As an experienced development partner and manufacturer with extensive material expertise, RAUMEDIC AG is ideally positioned to develop product-specific components that meet the future challenges of the pharmaceutical and medical technology industries. In fact, leading providers are already choosing these unique pure silicone syringe stoppers—ensuring safety not only for stoppers and seals but also for components in analytical devices, patch pumps, and many other drug delivery systems.
Summary
Key Advantages of RAUMEDIC Silicone:
- Up to 83% lower sliding friction than rubber, depending on application → virtually no stick-slip effect
- Complete elimination of silicone oil possible
- Storage range from -80 °C to +200 °C (including ULT)
- Ultra-pure material with minimal extractables
- Long-term shape stability, no cracking, no microparticles
- Skin-friendly and hypoallergenic
- Compatible with all standard sterilization methods
List of Potential Extractables
Do you need more information about potential extractables of non-sterile and ETO-sterilized RAUMEDIC silicone stoppers?
Request the extractable study according to BPOG right now!