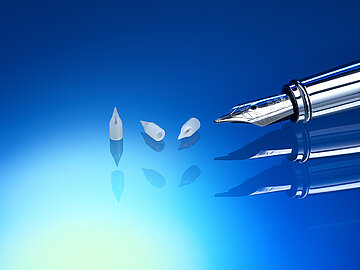
- Development
- Article
- Reading time: 10 min
Focus on Micro Molding
RAUMEDIC Focuses on a Complete Systems Approach to Micro Molding
The continually evolving demands of the Medical Industry constantly drive suppliers and manufacturers to expand their technical competencies into regions that they may have historically feared to tread. Doctors and surgeons are demanding instruments for less invasive procedures and quicker turnovers. Devices are becoming smaller and more complicated. Industry designers and procurement specialists are demanding smaller, higher precision components with exotic materials and tolerances that may not have been possible years ago. This trend in “Micro-Molding” processes and components advertised or written about in technical articles and industry publications has often led to confusion and to missed opportunities when it comes to supplier selections.
How to Define Micro Molding
RAUMEDIC defines true “Micro-Molding” in a few different ways. One would be part weight, with a typical range from 1 gram to smaller than 0.004 grams. Tolerances required are often much tighter than 0.001”. But more importantly “Micro-Molding” can be defined as components with sizes or tolerances so small that they are not able to be manufactured correctly, robustly, or with a high degree of precision using traditional injection molding equipment and standard thought processes. RAUMEDIC also applies the Micro-Molding thought processes to extrusion and tubing manufacturing. Defining the specifics of Micro-Extrusion as inner diameters of 0.004” with wall thicknesses of 0.002”. This can even apply to coating technology with micro-layers as thin as 0.0002”.
Think Small
To be successful with Micro Molding takes more than simply purchasing a small injection molding press and a microscope. All levels of the organization must make the decision to commit to success, at all levels of the manufacturing process. This must translate to a passion for problem solving, and thinking small, in the Micro Molding world. All phases of the process should be engineered to manage the specific sub-set of problems that comes with making Micro components. Careful though to resin selection, component design, equipment and molding processes, tooling construction, measuring equipment and even component handling and packaging are all critical. These may seem standard in today’s injection molding industry, but Micro requires specialized solutions to ensure success and a happy customer.
Involve the Manufacturer Early
The specific type and grade of resin should be selected with careful input from the material supplier and the manufacturers engineering resources. Semi-crystalline or amorphous resins, fillers and fibers, and even colorants can all have an impact on the product consistency required to meet critical dimensional requirements. Selecting the material appropriately is the foundation for the long term manufacturability. Use consistent amorphous engineering grade resins for tight tolerances. Apply fillers for added dimensional stability where necessary.
Following general part design principals are recommended for any successful part design. In Micro Molding, not only meeting these guidelines but exceeding them is a hard requirement. Slight areas of sink in ribs, slight warpage in sharp corners, or flowing thin to thick may cause slight problems in a large part. In a small part they can be disastrous and result in deformation that can exceed the allowable tolerance. Get your suppliers involved early in the design phase to ensure success and a robust design.
Tool construction is of the utmost importance as well. Traditional time tested tool construction methods can cause problems when tolerances and geometries are microscopic and critical. In fact this may even be the most important phase of the development project. It is critical to manufacture the tooling using processes that are able to create fine sharp corners, extremely flat surfaces, tricky geometries, and everything in the perfect detail required. The standard end mill and EDM need not apply!
Equipment selection is the next step in the development process. Many manufacturers now offer packages that are almost off the shelf for specialization in Micro Molding manufacturing. Make sure to involve the manufacturer early in the process. Be prepared to disclose shot weights, material selections, part size, and critical features. Shot control may exceed what is possible for a check ring screw. A plunger or ram may best fit your application. Consistency is the key to long term success.
100 % Control of Quality and Quantity
Now that you have molded a component, how do you know it is acceptable? Careful selection and possible investment in metrology and measurement systems processes will give you the data you need to know for sure. Equipment must be able to measure small dimensions, with small tolerances, and demand Gage R&R results better than 10%. Calipers and micrometers will not lead to positive results. Each component offers different challenges for measurement. But technology has come a long way in this area in the past 5 years. Laser scanners, CT scanning, non-contact optical vision systems are more readily available and all offer packages that can be customized and programmed for your specific need.
An area that may be often overlooked is packaging. It may almost be an afterthought for standard injection molding, but can cause many problems when trying to control delivery of Micro Molding components. Ensuring part counts are correct can be difficult when a month’s worth of production demand can fit into the palm of your hand. Traditional weigh scale verification certainly will not get the job done here. Certain automated systems can help with this as they tie directly into the press interface and rely on camera controls to verify count and quality. Rely on optics and on technology. Use small sealable bags or vails where appropriate. Segregate into small quantities when you can.
Communication is the Route to Success
Micro Molding is a challenging venture. But it can be done successfully. All interacting systems should be designed concurrently with careful thought to how all components interact within the manufacturing process. Positive communication between engineers, project managers, equipment suppliers, designers, molders, and quality inspectors is required for success. Designers and engineers should contact their supplier of choice early in the project. This will lay the roadmap required with there is little room for error in the Micro Molding world.